Polytetrafluoroethylene rubber composite bellows rubber hose
This wavy product is lined with PTFE anticorrosive coating and a soft rubber layer, which integrates the characteristics of the two layers of materials, so it not only has excellent anti-corrosion but also can be suitable for dislocation connection in various environments, which can make up for the shortcomings of longitudinal thermal expansion and cold shrinkage and transverse dislocation in the case of rigid connection of the hose.
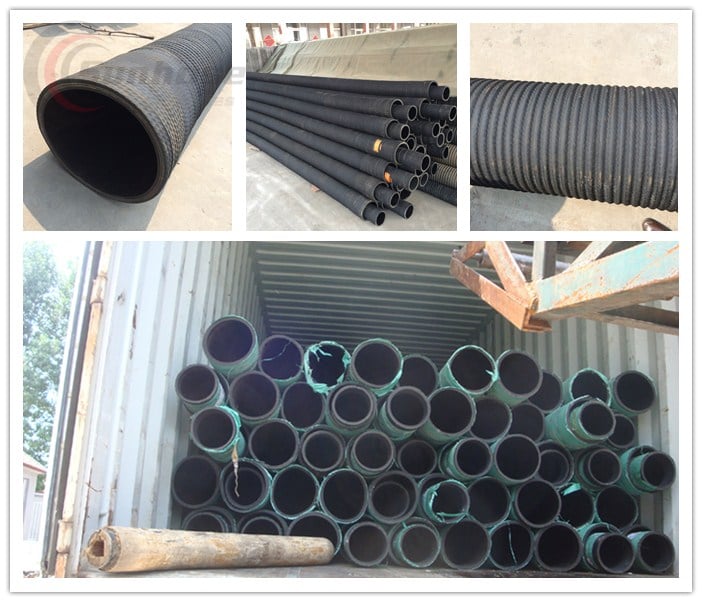
The main production steps are as follows:
The preform of PTFE wavy arm. The concrete process of pre molding by isobaric compression method is as follows: adding PTFE resin mold between the rubber bag and metal main die, pressing, holding pressure, releasing pressure, removing the rubber bag, trimming and PTFE bellows preform. The process parameters are as follows: pressing pressure 25 MPA, holding pressure 5 min.
Post-processing of PTFE bellows. The specific process is as follows: installation and setting of the tire, sintering, quenching, flanging, and trimming of PTFE bellows.
Sintering temperature and time are important process parameters. When the sintering temperature is below 300℃, the heating rate is 80 × 100℃/ h, above 300C, that is, the stage with the fastest crystallization rate of PTFE (315℃-320℃).
Heat preservation for 30 min, then 50C/h speed up to 380C60 min, out of the furnace rapid water quenching flanging temperature kept at about 327C, at this time PTFE softness is the most suitable for processing.
(3) Polytetrafluoroethylene/rubber composite bellows were prepared by composite with rubber. The specific process is as follows: PTFE bellows-surface activation treatment-coating treatment and rubber compound vulcanization-demolding-dressing-PTFE/ rubber composite bellows.
The purpose of activation treatment on the outer surface of PTFE bellows is to improve the interfacial bonding between Naphthalene sodium complex and rubber. After activation treatment, then coated with JQ-1 polyisocyanate adhesive (commonly known as Lexner gum), then combined with rubber, pressure heating vulcanization, demolding, and finishing to obtain the finished product.